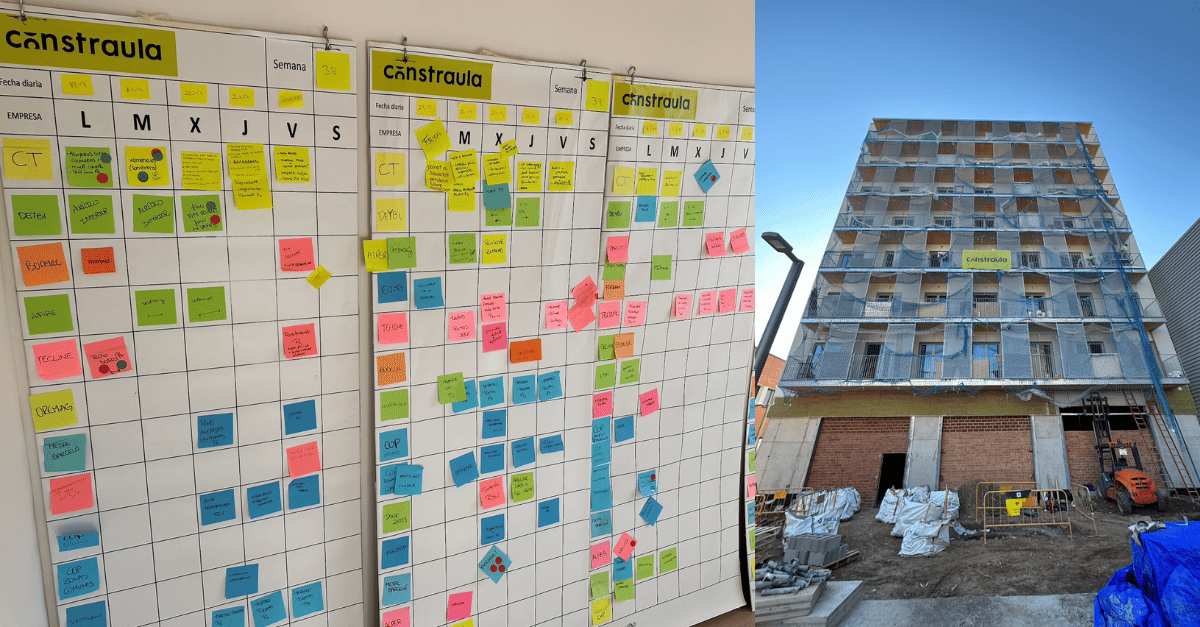
case study – thanks to lean thinking, this spanish construction company was able to deliver a challenging project in one year, well ahead of schedule. here’s how they did it.
words: jorge mercader, lean coach, and marc llopis, production manager, constraula
in recent years, construction sites have popped up all around the up-and-coming poblenou district of barcelona, transforming it beyond recognition. one of these construction sites, however, has a lean story to tell. a new 7-storey residential building was just completed. the project is funded by the city government and aims to offer much needed affordable housing in a neighborhood where the average cost of an apartment is €4,500 per square meter.
the project started in october 2022. we had until february 2024 to complete it, but we actually finished it ahead of time – one year after it started. this was in spite of a couple of hiccups in the first stages, when city hall made some changes to the original project.
the peculiar thing about the building is that it is made of wood – not a common occurrence in this part of the world, but an increasingly popular solution. constraula, the urban maintenance and city services company of the sorigué group, won the bid largely because their project entailed the use of this material, by far the most sustainable one can deploy in construction (the building even won the construmat sustainability award this year). it was our first project of this kind, but through research and a careful selection of suppliers we were able to make up for what we didn’t know.
this was also our first lean endeavor. last year, we decided to engage in a few lean training sessions (they were practice-based, using a construction simulation with lego blocks). we liked them so much that we decided to give the approach a go. and what better way to test it than using it in a soon-to-launch project? from day one, the team showed great enthusiasm and that was ultimately the reason behind our success.
of course, we relied heavily on last planner, which is the chief planning tool in a construction project, fostering collaboration and facilitate the elimination of waste. to that, we added other lean techniques, like 5s, daily management and scientific problem solving.
coordinating work
what lean brought us was collaboration between people and all the different subcontractors. everyone was involved in the initial planning of the construction project and attended the follow-up meetings week after week. we soon found out that lean allows you to discover problems sooner and identify all the co-dependencies that – if ignored – can lead to big problems and substantial delays in the delivery of the project. the great thing about having a systematic approach to problem discovery, analysis and resolution was that, when we encountered problems on the first floor, we already knew we’d be likely to encounter them in the other floors too. this made us more prepared to deal with them, as we used kaizen to make all the improvements needed and prevent problems from reoccurring.
the place where problems were raised and discussed was our weekly meeting, during which we reflected on what happened on the previous week, on the issues we encountered (as well as how many tasks were completed and how many were not), and looked ahead of the following week.
our guide through it all was the masterplan. to design the process and determine the right sequence of activities, we first worked with the core project team, which included the site manager, supervisor, and production manager. we made estimations based on our experience and knowledge of what each of these processes would entail. then, we put the plan on a big board and discussed it with our industrial partners. this took three or four sessions. it is important to invest time in figuring out the process and the sequence up front, so you don’t have to do it “on the go” and likely engage in time-consuming and wasteful replanning.
next to our masterplan board, we had four others – the “look-ahead boards” – referring to the next four weeks. they highlighted the key tasks that needed to be carried out and specified by what trade/company and by what date they had to be completed. the look-ahead boards gave us a very clear representation of the sequence of the work, day by day, and told everyone what they are supposed to do, and by when. lean visual management made for extremely smooth communication throughout the process.
in terms of performance indicators, we focused on the essential ones, avoiding unnecessary complexity. we primarily tracked two: the attendance of industrial partners in our meetings and the completion rate of weekly tasks. our tracking tools were straightforward excel spreadsheets. each week, we assessed the planned tasks’ completion percentage. when tasks were not fulfilled, we conducted a detailed analysis of the root causes of the non-completion, so we could address them and fix the problem.
for this project, we had 13 trades – our “providers”, so to speak. not all of them worked on the building the same time, of course, but this didn’t make coordination any easier to achieve. luckily, we had our lean system, which allowed us to create that coordination, suggesting the right order in which each task should be completed so that the following subcontractor could come in and do their part without obstacles. to further support the work of subcontractors, we also deployed 5s to maintain order and tidiness on the site: that way, each trade could work in the best possible conditions.
besides our masterplan and our weekly planning, we also have to manage our day-to-day activities. whenever unforeseen factors, like the weather, popped up and threatened to hinder our work, potentially causing us to fall behind on our schedule, we tried to think creatively and look for a quick solution. for example, diverting resources to another task that, though not timed ideally, could still be done without disrupting the overall sequence of the work.
this project reminded us of how critical good planning and coordination are in construction. the fact that communication flowed seamlessly and that we understood the benefits of working with the work of others in mind made it possible to solve pretty much any problem we faced. when the subcontractor responsible for the thermal insulation of the façade told us they wouldn’t have enough people available to complete the job in time, we immediately reached out to the architect and determined that we could still install the windows and ask the subcontract to come in for the finishings later. this countermeasure may not be the most common way of doing things, but it allowed us to not interrupt the work and stay on track. another example of successful coordination was the work we did to organize the delivery of wood all the way from austria: we talked to the supplier early on and knew exactly in what order the trucks would arrive and what modules they carried. based on this experience, in the future we’ll try to only work with those subcontractors and suppliers that are willing to align with our way of working.
success factors
wooden structures are faster to assemble and allow you to carry out different tasks at once, and that’s certainly one of the reasons behind our early delivery. but we have no doubt that lean thinking is the other reason: it showed us how to break the work into small bits that were easier to see and manage, and ultimately allowed us to work with subcontractors as one team. it was incredible to see the synergies that emerged during the weekly meetings, as different players tapped into their experience to help each other out and discuss the best way forward.
to complement our work of process optimization, we also put a lot of emphasis on the people making up the wider project team. from day one, we looked for agreement among the different players, we set clear objectives and expectations, and defined our values, determining how we want to work and manage things. for us, it was important to create accountability to ensure everyone was aware of how their timeliness positively impacted the work of other subcontractors and the progress of the overall project.
it is clear to us that lean thinking brings benefits to everyone involved, and we think our subcontractors realized that, too. to know exactly what they were supposed to do and when meant they could make a smart use of their resources and made everyone’s work easier – which is proved by the fact that stress was absent from our construction site, and we always felt in control of the situation. this speaks volumes about the value of lean thinking in construction, something that is so clear to us that we are determined to use the methodology in all our future projects. we wouldn’t know how to get back to the way things were!
the authors
jorge mercader (right) is a lean coach