作者:李兆华
全文字数:1425
阅读时间:5分钟
丰田生产方式的源流在于满足顾客,「」。但?
常见的对策是以更多的资源与库存来因应,但这不是丰田一贯的方法,2000年间我参加丰田生产调查部所主办的tps研修结束前,当时的斋藤彰德课长给我们他如上图的心得,协力厂导入tps的7步骤。迄今我仍是这么做,且屡试不爽。
这步骤背后的道理仍是:
1. 满足顾客。
2. 凸显与顾客需求不一致的问题。
3. 持续改善。
以下特别提示在实务上被人忽略,但丰田却最重视的步骤1, 2, 3,这也是为什么丰田生产方式的指导者观察现场时,都从出货场看起。
步骤1. 要备好要出货的成品,以保证能准时交货
步骤2. 模拟顾客生产现场的需求来领货,以更仔细地凸显供需不平衡的问题
步骤3-6,都是被常提到的tps方法,此处省略
步骤7. 当顾客的需求稳定之后,可以减少为对应顾客需求变异的缓冲库存。丰田的供货商大都没有这缓冲库存,但有些为了自家原因,甚至天灾而准备的安全库存。
企业越小,越会受到顾客需求变动的影响。但仍须准时交货,为此简直是买卖双方的梦魇。大家都知道需要买卖双方的合作,但谈何容易?
曾任丰田汽车副社长的友山茂树先生在生产调查部时,曾有协助一家夫妇两人的二阶以后供货商的案例,也可说明tps为何坚持缩短前置时间,在自家可以对应的范围内,吸收、协助顾客因应订单的变异(顾客的顾客也在无厘头的变异交期)。详《丰田传》12章。
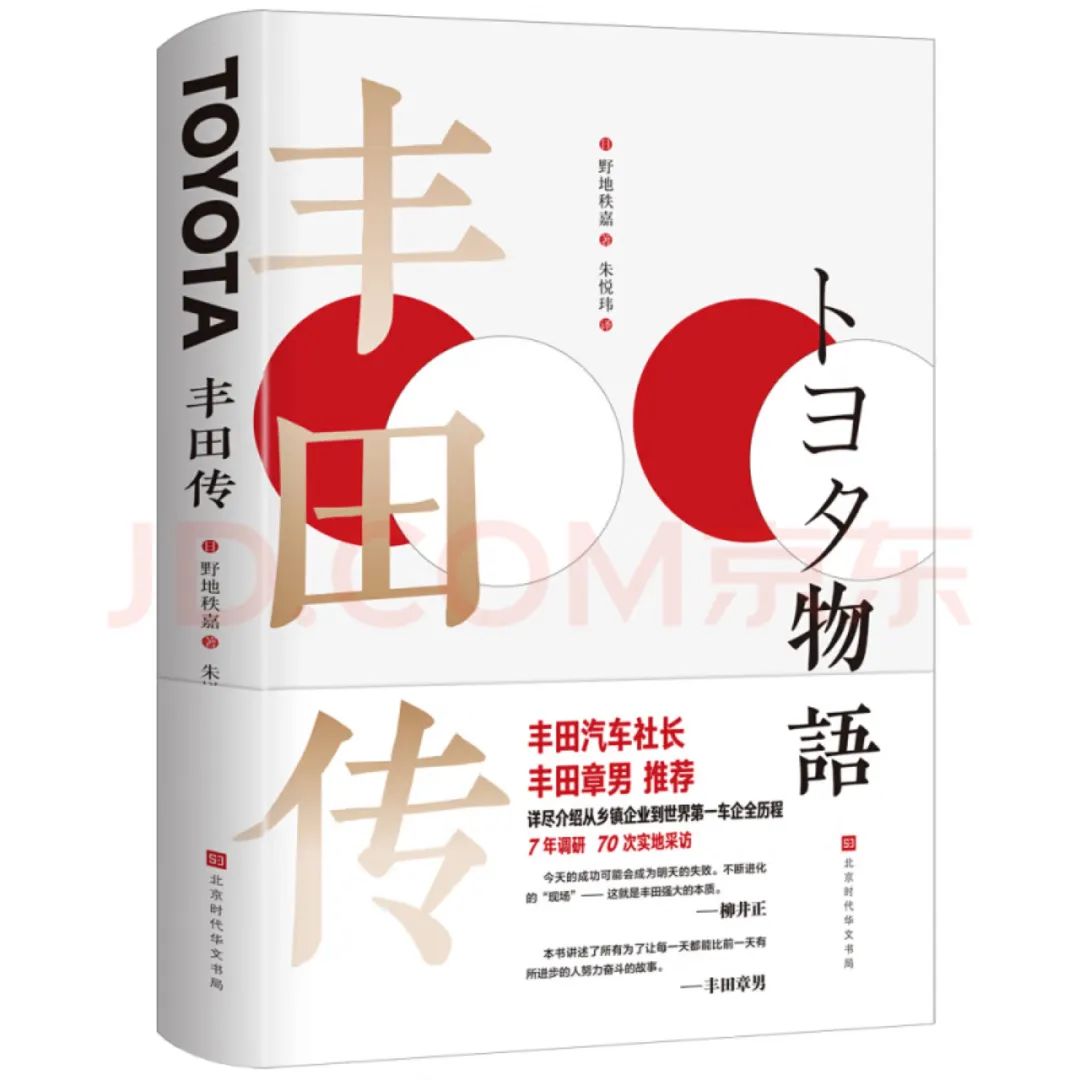
1 缩短前置时间
客户在订单上做稍微变更,就经常让老伯老妈苦不堪言。两个人用尽心力在工作,但是电话一来,不是「要增加数量」,就是「减少数量」。面对交货前的变更,是中小企业的宿命。由于「变更次数太多,所以老伯老妈只好总是准备12个或15个,来应付10个的订单,结果原料增加,又浪费人工。
因此,他对两人说「我们来缩短前置时间吧」,如果客户最晚在交货前一星期会变更订单的话,那就在交货的一星期前再开始做就行了。也就是说将前置时间缩短到订单确定后,来得及交货前的时间。同时,与客户负责人员的联络要更密切。再三与对方确认,实际需要几个、最晚什么时间要,以此提高接单的精确度,减少浪费的工作。
2 减少库存
缩短前置时间,减少不需要的库存。为了将两星期以上的前置时间,缩短到五天以内,需减少模具更换时间,和机器的周期时间,建立小批量生产的机制。规划按种类分类的店面,贯彻先入先出的原则,库存一减少,不知为何连质量都改善了。
3 每一个托盘都挂上看板
藉由看板的循环,只生产所收到看板的部分,作为后补充生产。大量品按一天的批量每天准备,少量品按五天的批量生产,每星期准备生产一次。
4 导入模式生产
模式(pattern)生产就是固定一个模式,例如将a做到这里后,制作b,然后接下来做c。用一台树脂成形机,生产成形温度各不相同的多种制品时,若是能按温度上升的顺序生产,效率会提高。因此,将收到的看板也按着这个顺序排列,进行模式生产。
简言之,就是将大野初期在丰田工厂执行过的精华,套用到小工厂中。只靠整理整顿,工作就有了进展,并且有了成果。这么一来,老伯和伯母工作也来劲儿了,他们甚至还说:「请再多教我们一点。」
综观斋藤与友山的步骤,包括了大部分丰田生产方式的改善实务。当自家的改善可以满足顾客变异的需求时,期待顾客改变的重要性已不复以往,甚至于因为自己是供货商的顾客,自家稳定的生产使得要求供货商改善的需求也降低了。
改善从自己做起,若供应链上的所有成员都这么做,必将成为顾客喜欢的坚强团队。
以往有关于《丰田传》的专栏: