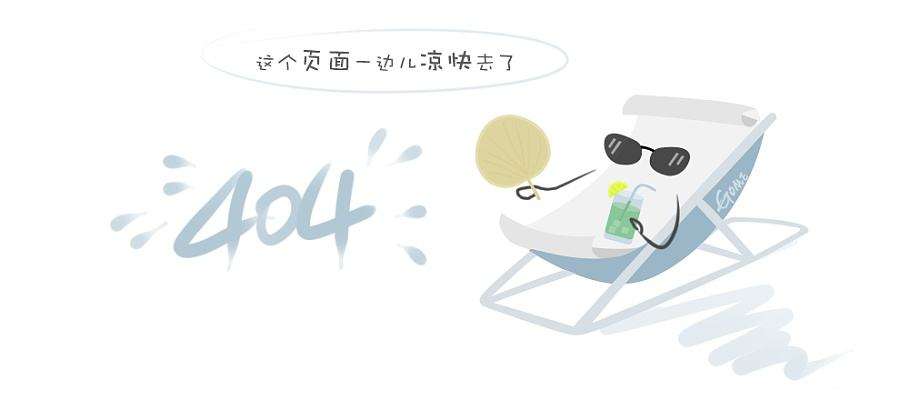
lean lexicon
using an extended value-stream map, a breakthrough tool for improving extended value streams, dan jones and jim womack demonstrate how 90% of the actions and 99% of the time along a typical value stream can consume resources, but create no value for customers.
more importantly their workbook seeing the whole, which received a shingo research prize in 2003, shows companies how to fix the problem.
jones and womack, co-authors of machine that changed the world, lean thinking, and lean solutions, introduce the new mapping methodology in seeing the whole. the workbook shows managers and engineers how to use mapping to count and analyze all the steps and the time needed for a product to go from raw materials to finished goods in a typical value stream across multiple plants.
to clearly illustrate the mapping process in action, the book uses a simple example, a windshield wiper assembly, as it moves through eight separate facilities and four companies in two countries, starting at a finished goods distribution center and moving upstream through manufacturing and raw material businesses.
“the experience of our sample product illustrates what we have seen repeatedly between facilities and firms — sets of actions extending for days, weeks, and even months, most of which consume resources but create no value for the customer,” said womack, lei founder and chairman. what they typically see:
·90% of total steps are waste from standpoint of end customer.
·99% of throughput time is wasted time.
·demand becomes more and more erratic as it moves upstream, imposing major inventory, capacity, and management costs at every level.
·quality becomes worse and worse as we move upstream, imposing major costs downstream.
·most managers and many production associates expend the majority of their efforts on hand-offs, work-arounds, and logistical complexity.
·99% of throughput time is wasted time.
·demand becomes more and more erratic as it moves upstream, imposing major inventory, capacity, and management costs at every level.
·quality becomes worse and worse as we move upstream, imposing major costs downstream.
·most managers and many production associates expend the majority of their efforts on hand-offs, work-arounds, and logistical complexity.
a simple visual tool for action
the mapping methodology takes managers step-by-step through an improvement process that converts the traditional value stream of isolated, compartmentalized operations into an ideal future-state value stream in which value flows from raw materials to customer in just 6% of the time previously needed. the dramatically improved value stream also eliminates unnecessary transport links, inventories, and handoffs, the key drivers of hidden connectivity costs.
the mapping methodology takes managers step-by-step through an improvement process that converts the traditional value stream of isolated, compartmentalized operations into an ideal future-state value stream in which value flows from raw materials to customer in just 6% of the time previously needed. the dramatically improved value stream also eliminates unnecessary transport links, inventories, and handoffs, the key drivers of hidden connectivity costs.
“taking a walk together through all the facilities down a value stream is always an eye opening experience,” said jones. “this tool provides a method for taking action together to do something about it.”
lei popularized the concept of value-stream mapping with its initial workbook, learning to see (lts), which has now sold more than 100,000 copies in ten languages. lts teaches business people to see clearly the value stream consisting of all of the actions required to move information and materials for one product family through one facility. after identifying the current state of the value stream, lts shows readers how to create a future state with much less waste, much higher quality, and more rapid response to changing consumer demand.
in seeing the whole, jones and womack expand the field of view from the individual facility to the entire value stream from order to delivery.
in addition, the extended mapping method clearly shows demand amplification of orders as they travel up the value stream, steadily growing quality problems, and steadily deteriorating shipping performance at every point up the value stream from the customer. collectively, the wasted actions and time plus the noise in the information stream and the quality and delivery deficits, present a tremendous opportunity for the four firms sharing this value stream. they can create a win-win-win-win-win future in which everyone, including the end consumer, can be better off.
doing this requires the creation of a value-stream team and the progressive achievement of a series of future states, culminating in an ideal state in which a very large fraction of the waste had been removed. the objective of seeing the whole is first to raise consciousness about the potential gains and then to provide a simple method for forming an appropriate team to identify the current state and to achieve future states leading eventually to an ideal state.
for the tens of thousands of users of value-stream mapping at the facility level, seeing the whole provides the logical next step, by extending the field of view all the way up and down the value stream. and for purchasing and supplier development groups currently focused on improving isolated points along the value stream, seeing the whole shows how to see and then how to improve the entire stream. “the challenges of doing so are great but the rewards are truly enormous,” said womack.
the information in the 96-page book is supported by multiple diagrams, charts, and new mapping icons for extended value streams. the main sections of the book are:
·introduction: changing your focal plane
·getting started
·the current state map
·what makes an extended value stream lean
·future state 1
·future state 2
·the ideal state
·achieving future states
·conclusion
·getting started
·the current state map
·what makes an extended value stream lean
·future state 1
·future state 2
·the ideal state
·achieving future states
·conclusion