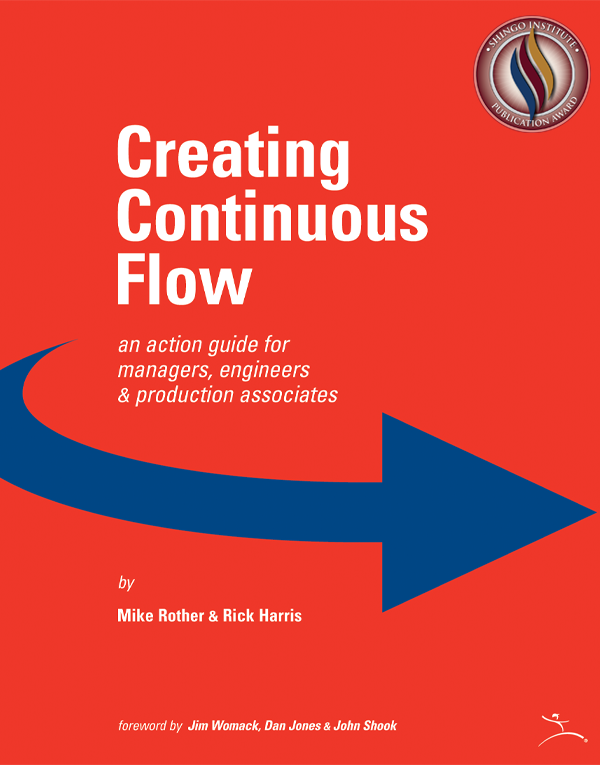
creating continuous flow
shingo research and professional publication award recipient
this workbook explains in simple, step-by-step terms how to introduce and sustain lean flows of material and information in pacemaker cells and lines, a prerequisite for achieving a lean value stream.
a sight we frequently encounter when touring plants is the relocation of processing steps from departments (process villages) to product-family work cells, but too often these “cells” produce only intermittent and erratic flow. output gyrates from hour to hour and small piles of inventory accumulate between each operation so that few of the benefits of cellularization are actually being realized; and, if the cell is located upstream from the pacemaker process, none of the benefits may ever reach the customer.
this sequel to (which focused on plant level operations) provides simple step-by-step instructions for eliminating waste and creating continuous flow at the process level. this isn’t a workbook you will read once then relegate to the bookshelf. it’s an action guide for managers, engineers, and production associates that you will use to improve flow each and every day.
creating continuous flow takes you to the next level in work cell design where you’ll achieve even greater cost and lead time savings. you’ll learn:
- where to focus your continuous flow efforts
- how to create much more efficient work cells and lines
- how to operate a pacemaker process so that a lean value stream is possible
- how to sustain the gains, and keep improving
creating continuous flow is the next logical step after . the value-stream mapping process defined the pacemaker process and the overall flow of products and information in the plant. the next step is to shift your focus from the plant to the process level by zeroing in on the pacemaker process, which sets the production rhythm for the plant or value stream, and apply the principles of continuous flow.
every production facility has at least one pacemaker process. the pacemaker processes is usually where products take their final form before going to external customers. it’s called the pacemaker because how you operate here determines both how well you can serve the customer and what the demand pattern is like for your upstream supplying processes.
how the pacemaker process operates is critically important. a steady and consistently flowing pacemaker places steady and consistent demands on the rest of the value stream. the continuous flow processing that results allows companies to create leaner value streams.